Lost-wax casting: Everything you need to know
Lost-wax casting: Everything you need to know
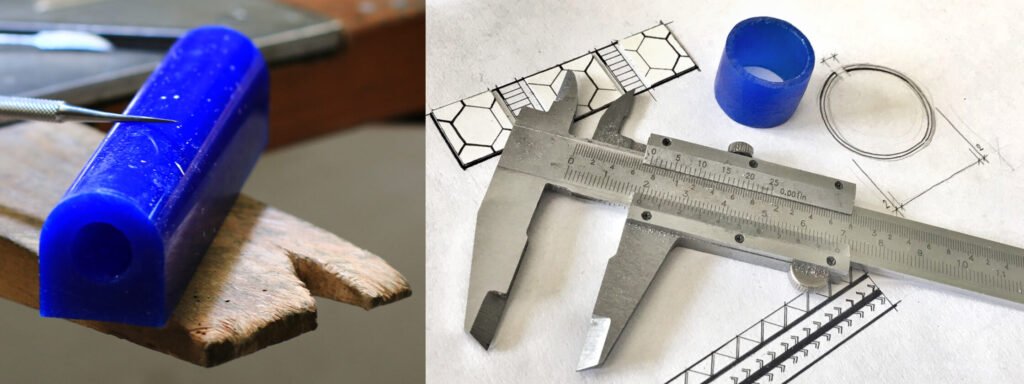
What is the purpose of lost-wax casting?
At Mayari jewelry, one of the methods we use to create jewelry is called lost-wax casting* (aka “cire perdue”). *also it is presently used interchangeably with investment casting
It is an ancient process (and we do respect jewelry making traditions) that casts a metal sculpture from an original sculpture made of wax. The lost-wax method has been used since 3000 B.C. (and it has sustained few changes since then) to capture the stories of ancient cultures and religions throughout history. Isn’t it fascinating?
The casting process for lost wax casting involves multiple steps that begin with the creation of the pattern, or master, from wax (and then sterling silver). Thanks to the lost-wax method we can recreate all parts of our designs with precision.
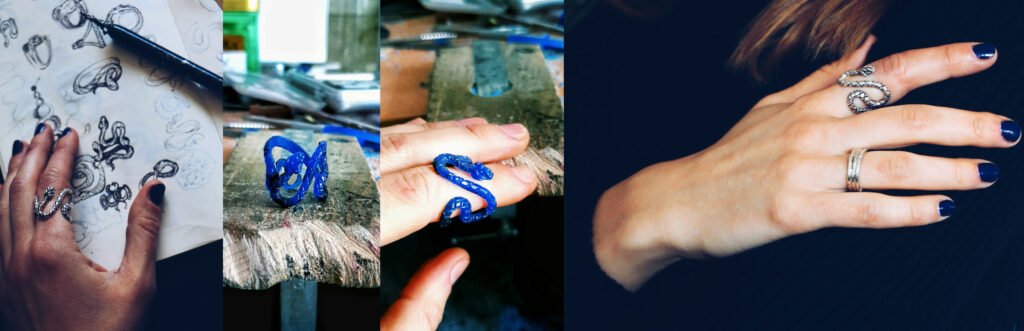
Our process of jewelry making:
inspiration – idea – sketches – more sketches – wax carving – wax mold fabrication – casting – polishing

Major steps of the lost-wax process
Creating a prototype
1. Detailed freehand sketches on paper (top/ side/ front views & 3D) and all the measurements for the final design.
2. A well-detailed wax model of the figure is created. And our model is now ready for casting!
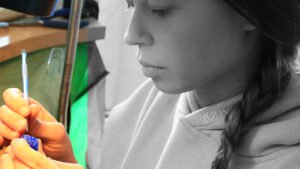
3. Later the wax is assembled on a runner system (¨tree¨).
4. Then investment plaster is poured into the cylinder and over the wax model.
5. The flask is heated in a kiln. The wax is melted out and forms a cavity where the metal flows in.
6. The silver grain is placed into the crucible to melt.
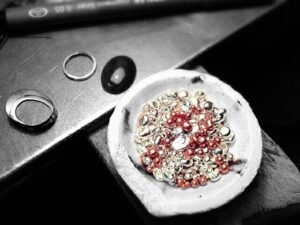
7. Molten silver (or any other metal) is then poured into the cavity. The flask is now filled with silver.
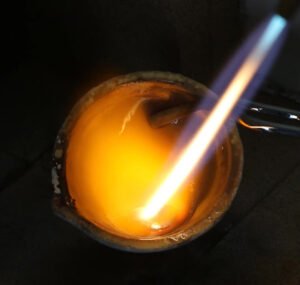
8. Then we dissolve the investment plaster.
9. The parts are cut from the ‘tree’.
10. The silver model is then filed and buffed to remove scratches.

Making a rubber mold
1. And now we are ready to create a vulcanized silicone rubber mould around the silver prototype. Modern synthetic rubbers have been developed to capture very fine details of a model.
2. We attach the sprue to the heaviest part of the prototype and then put it in a suitable mold frame.
3. Now it’s time to start packing the mold with layers of rubber. And when it’s done the mold is vulcanized in a machine that modifies rubber with heat and pressure.
4. The mold is cut into two halves, allowing the model to be removed.
5. Now we are ready to recreate the prototype. Hooray!
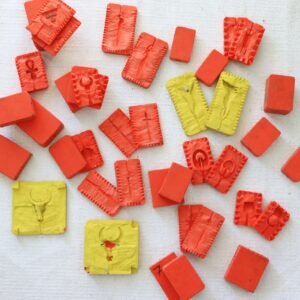

Recent Posts
OUR NEWSLETTER
Subscribe to our newsletter and get 10% off your next purchase!
Lost-wax casting: Everything you need to know Read More »